Member Interview
Scott Wexelberg
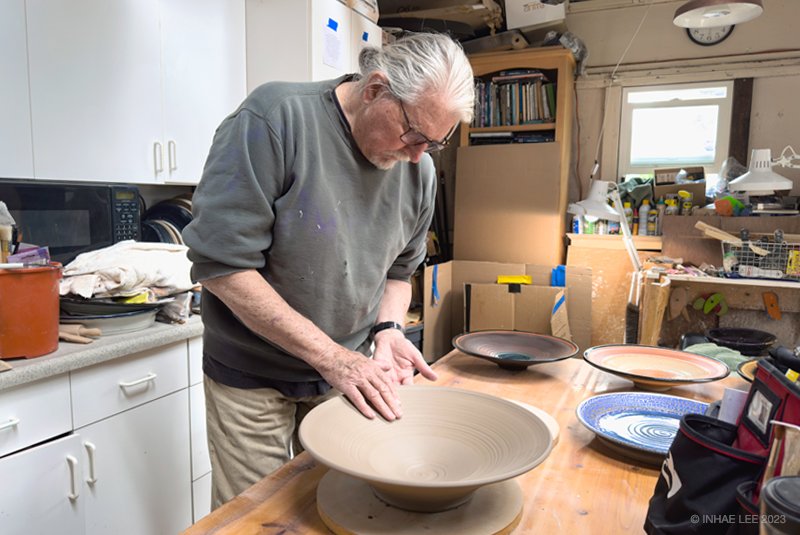
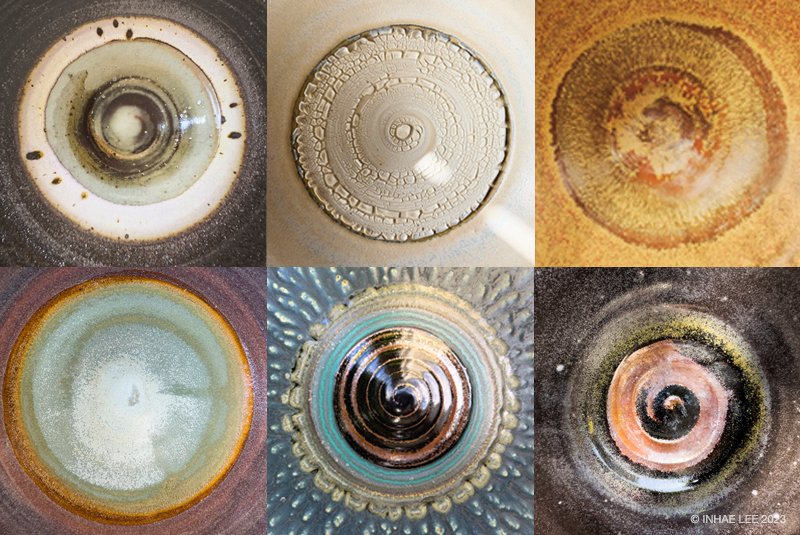
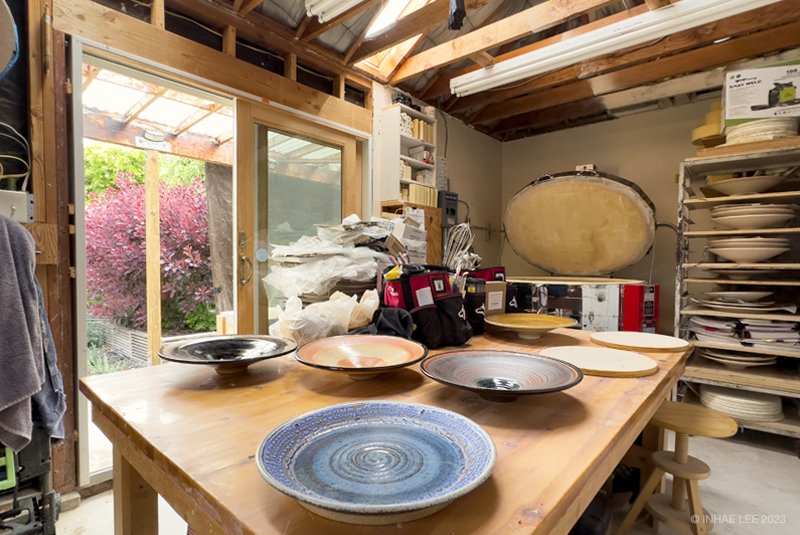
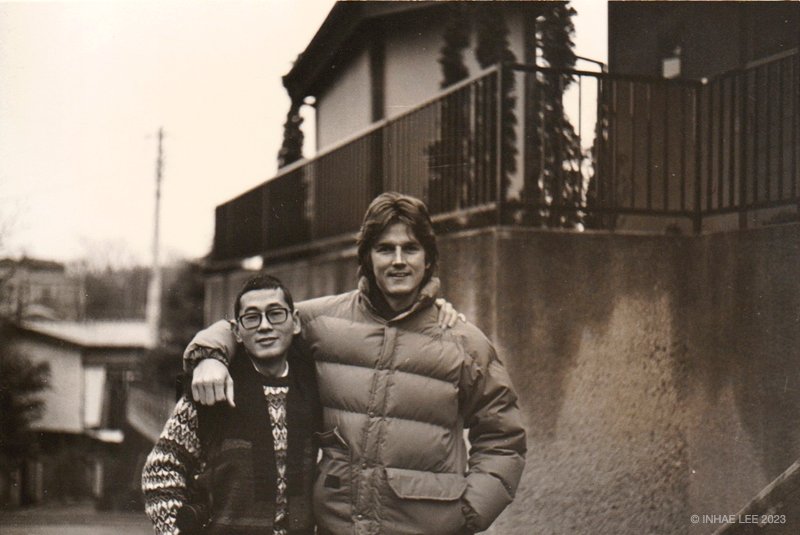
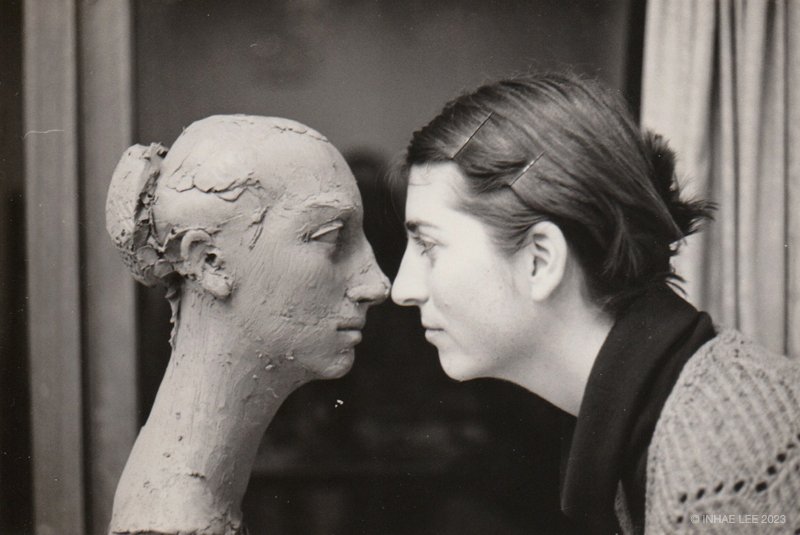
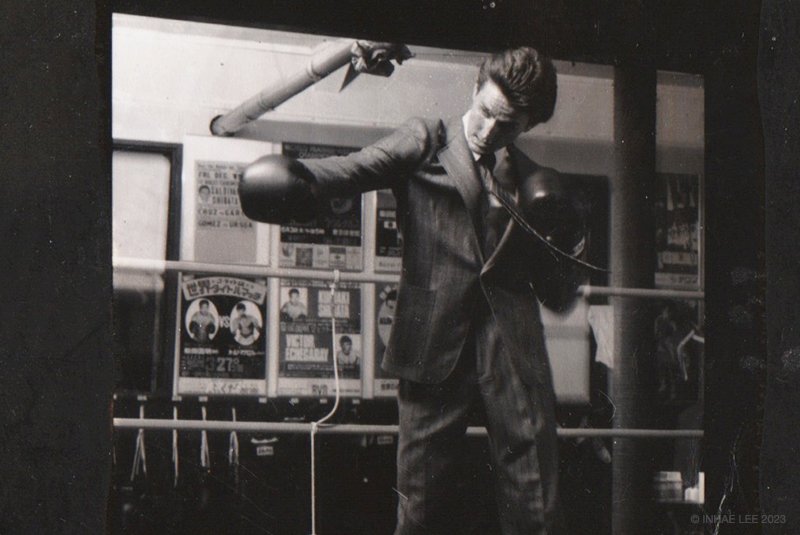
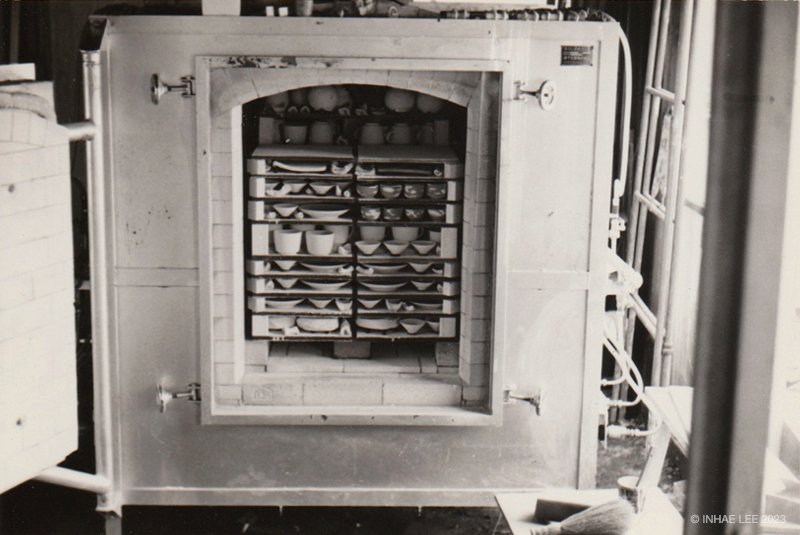
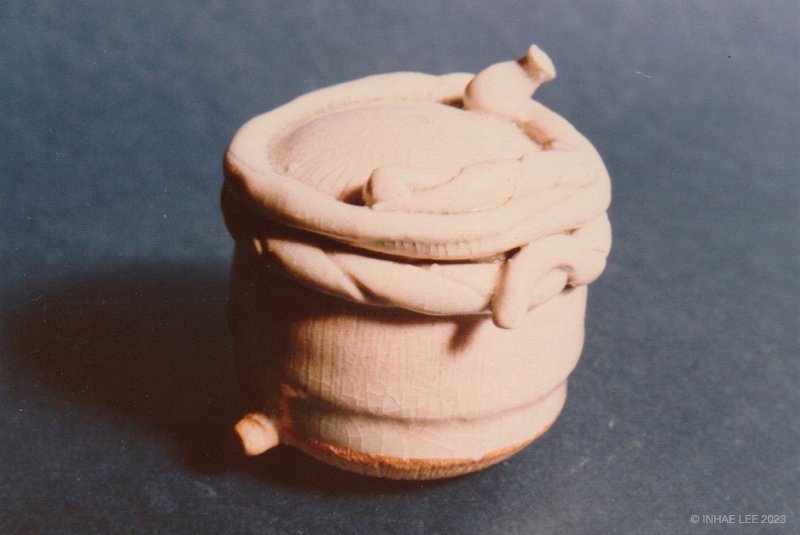
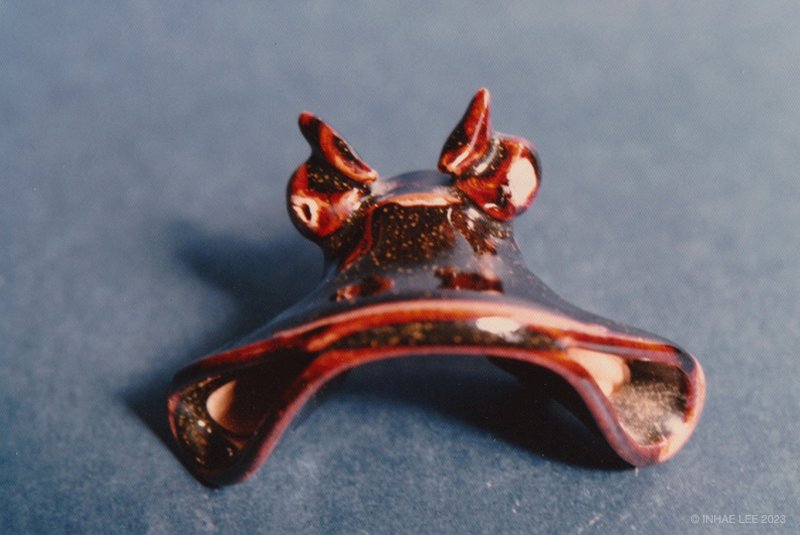
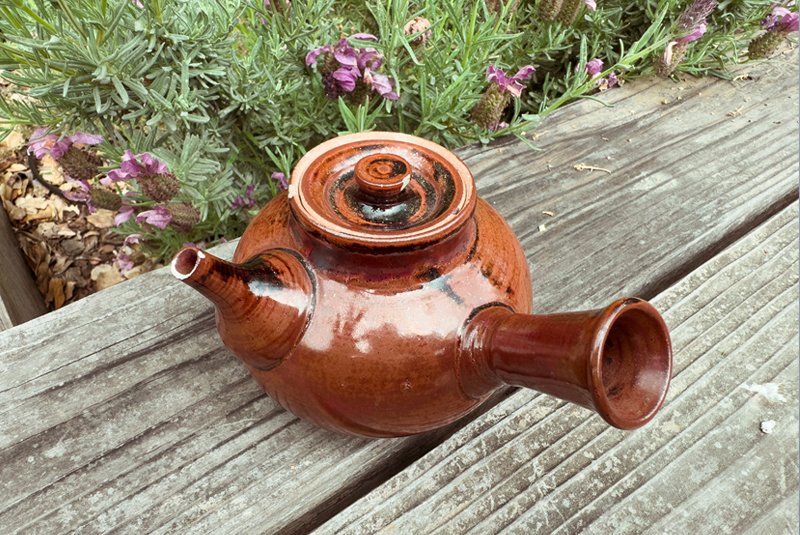
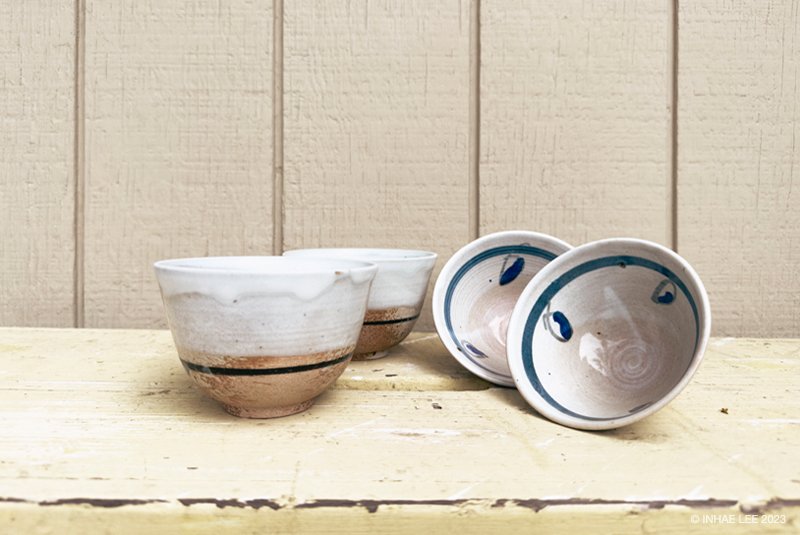
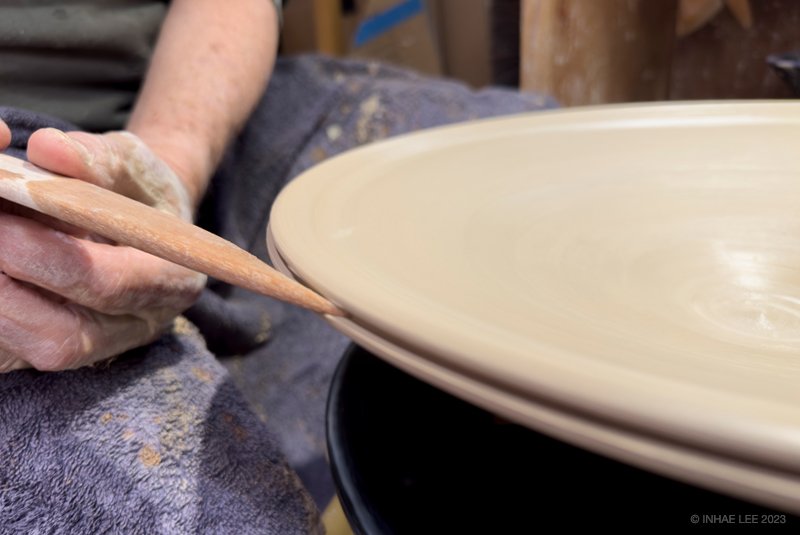
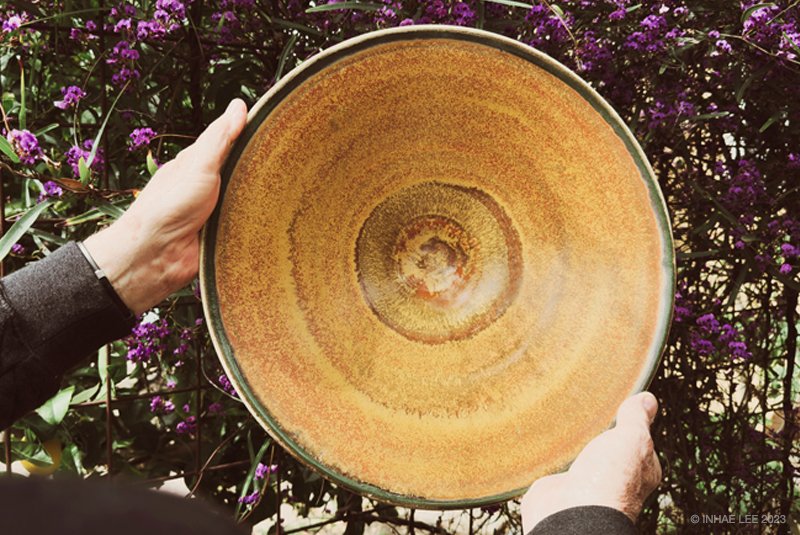
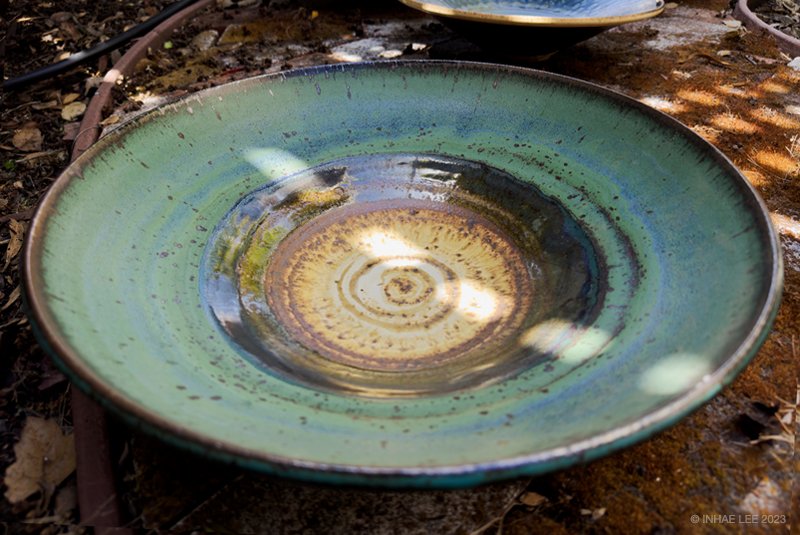
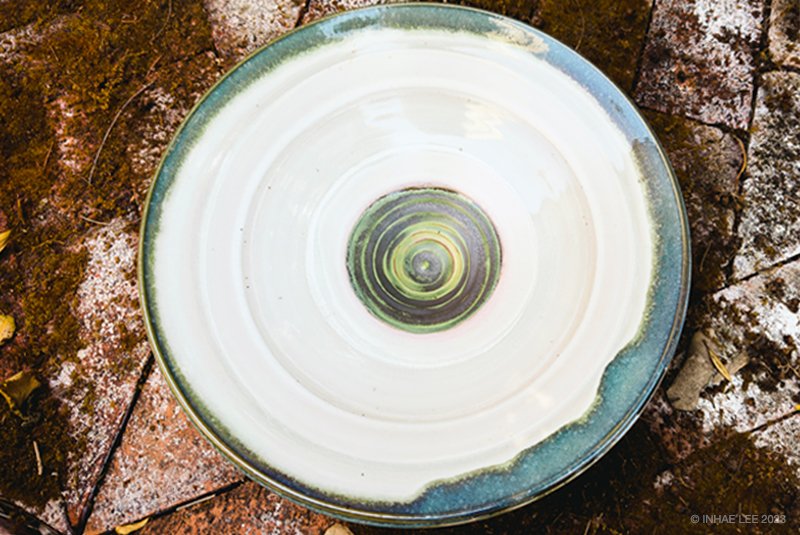
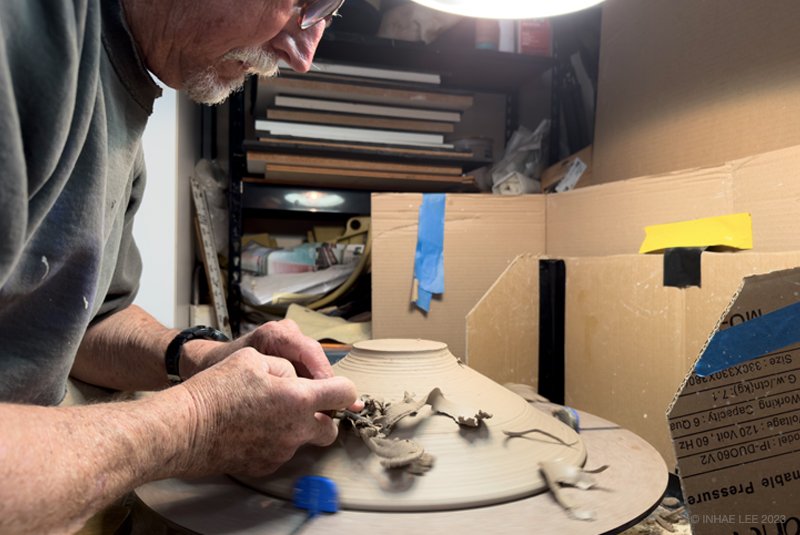
Hello there! I’m...
My everyday occupation is...
I’m a DAD, a Husband, and an Artist. I was a Builder for 42 years.
How did your everyday occupation influence or inspire you in ceramic work...
Most of my career, I was a hands-on craftsman (My motto was,“Head, Heart, Hands!“). Working as a manager for ten years, I discovered I was better at handling detail than most traditionally trained people, thanks to my art background. Consequently, I was able to appreciate and make important the smallest detail in my building work.
Today, I take my time in forming the feet of my large plates and bowls.
I’ve been doing pottery since...
I started working in clay at Santa Rosa College in 1971. In those days I was attending Cal State LA, but wanted to transfer to Sonoma State. I went “Up North” and enrolled in Santa Rosa Jr. College. I took one clay class and was “hooked“. Serendipity!
After a semester at the Jr. College I was allowed to transfer to Sonoma State. I graduated with a BA in Art in 1973, with an emphasis in Ceramics and Painting.
I would describe my work as...
I like to think of my work as Functional Art. I make large colorful pieces, (plates and bowls), that function well as useful tableware and look terrific on a wall or displayed on a plate stand.
What was the first memorable clay piece you made...
I lived and worked in Japan for 2 1/2 years, (I supported myself by teaching English and Fashion Modeling). I found a ceramic teacher named Manabu Sakai, and worked with him in his Yokohama studio for 2 years. The pottery wheels in Japan turn in the opposite direction from the American wheels. I had to re-learn how to throw backwards.
One of the pieces I was required to make was a Kyusu: A small one-handed tea pot. The normal Kyusu size was very small in relation to the size of my hands. Along with the handle, spout, interior tea leaf screen, and body, the small Kyusu was difficult to throw and assemble. So for me, the Kyusu was the piece that was most memorable.
What inspires you the most – Form, Glaze, Firing...
For me, size and glaze formation are the most inspirational. I like to make large bowls. After the glaze firing, I enjoy looking at how the different applied glazes flowed together during the Cone 10 Reduction firing. Not all the glaze combinations I apply work well, but when they do, they are terrific! The large size of the bowls draw me “into“ them, I want to BE in the bowl.
You went to live in Kawasaki, Japan in the mid-70’s for 2 1/2 years. Could you share with with us briefly about your experience in learning pottery abroad...
In relation to Ceramics, the Sensei (Teacher) to Deshi (Apprentice) relationship is very structured. In general, the Sensei is considered to be way above the Deshi in the social hierarchy. Many times, when my Sensei and I were out socially, he would demonstrate how much higher he was in the social order than I was. When my Sensei and I were alone together in the studio, this need to demonstrate higher status was rarely exhibited. For an American Male, like me, this need to demonstrate a higher social status was irritatingly accommodated.
A piece of advice for working in ceramics that helped me a lot was...
Slow down! Slowing down and being patient has been the hardest thing to do – but it works!
Artists I admire...
Phil Rogers, Mark Rothko, Lucie Rie, Toshiko Takaezu, Shōji Hamada, Warren Mackenzie... ...“An artist who seeks to create beauty through a utilitarian object.”
If I could pick only ONE clay tool for the rest of my life, it would be...
I’d have to stick with the electric Potter’s wheel. It’s such a pleasure handling the clay when it is spinning....that’s when the clay is cooperating, of course.
What was the least practical pot you made and the reason...
Several years ago, I was trying to throw a very large Charger Plate. I wanted a “canvas“ to apply various glazes to. The large Charger form, 18” diameter turned out to be very difficult to dry, bisque, and glaze fire. The charger kept warping, cracking, and blowing up!
Today I throw plates that are a little smaller around 16”. I dry my plates very slowly, it takes about 2-3 weeks for my plates to dry out, I slow bisque fire these large pieces. Glaze firing is still a hit or miss process, often the Chargers warp out in the Cone 10 Reduction firing. I’ve had to learn how to deal with the disappointment I feel when the large pieces come out of the Glaze Kiln badly warped, so it goes...
Interview article and photography by Inhae Lee